As digitalization of the fashion industry progresses, we hear more and more often the words Mechanical Parameters, or sometimes the Physics of digital materials. Regardless of how they are called, Mechanical Parameters play a key role in the digital fashion workflow, especially when designing and prototyping new garments. This post will explain what exactly are Mechanical Parameters and why they are important, but also why they are hard and expensive to acquire, and what can be done about it.
What is a Mechanical Parameter?
Generally speaking, a Mechanical Parameter is a number that characterizes the behavior of mechanical phenomena, tying a theoretical description to an experimental observation.
Imagine a spring. In its simplest form, the spring will exert a pushback force that is proportional to the amount of compression of the spring. The more you compress the spring, the more it pushes back, and this is true for all springs. However, not all springs are equal: for the same compression, some springs will provide more pushback, and others less. We say a spring is “stiffer” when it comparatively exerts more force, and its unique “stiffness” is what distinguishes it from another one. The “stiffness” of a spring is therefore the Mechanical Parameter of the spring: it can be measured, it is specific to a given spring, and it fully characterizes the spring. If we know how the spring works in theory, and we know its Mechanical Parameter, we can predict what force it will exert for a given compression distance*.
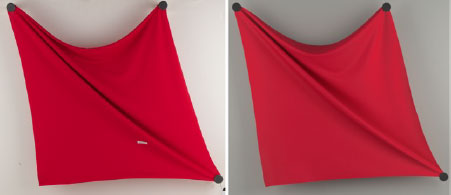
Good Mechanical Parameters are paramount for true to life draping in digital fashion.
Left: real photograph. Right: digital twin by Seddi.
Most elastic materials follow the same principle, and fabric is no exception. While a spring is basically one-dimensional (you can only pull or push along the axis of the spring), a piece of fabric is three-dimensional, so you can stretch it in different directions, but you can also bend it. Each of these forces, be it stretching or bending, has one or several Mechanical Parameters that characterize how stiff or compliant the force will be. A woven fabric, for instance, will usually be quite stiff if pulled along its warp direction, because it’s one of the directions of the yarns, and yarns are usually almost inextensible. The Mechanical Parameter for stretching in the warp direction for a woven piece of fabric is therefore usually quite high. On the contrary, it is very easy to bend most fabrics in any direction. The Mechanical Parameter for bending in the warp direction will therefore be quite low.
* If we want to get a bit more technical, the simple spring mentioned above is called a linear spring, and is a favorite among physicists because it behaves in a very simple and predictable way, following Hooke’s law: F = K𝑥. Here F is the force exerted by the spring when compressed by some distance 𝑥. And K is, you guessed it, the stiffness of the spring, the Mechanical parameter that characterizes it. Soft? Hard? It all depends on the value you give to K, because the rest of the formula to compute the force is exactly the same for all the linear springs out there
Why do Mechanical Parameters matter for Digital Fashion?
The fashion industry is seeing a widespread adoption of digital tools. In particular, 3D CAD allows the design of garments or even entire collections quickly and efficiently by avoiding or drastically reducing the need to manufacture physical prototypes. Yet, this is only possible if digital garments can produce true to life drapes and are exact digital twins of the physical garments they aim to dematerialize.
Enter digital materials and, with them, Mechanical Parameters. You want digital silk to behave like silk and not denim. And, ideally, a 255gsm CO/EA Denim and a 308gsm CO/EA Denim would behave differently, both in the real and the digital worlds. While all fabric materials are governed by the same stretching and bending forces, they each have very specific Mechanical Parameters to characterize those forces and give them that unique, distinguishable behavior that the designer is looking for. Without properly captured Mechanical Parameters, specific to each fabric, true to life drapes are impossible to achieve, and 3D CAD loses its most important asset: predictivity. Having complete and accurate Mechanical Parameters is therefore paramount to make the most out of digital fashion.
Why are Mechanical Parameters hard to get, and what can be done about it?
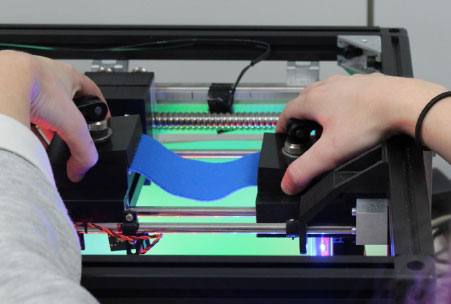
An operator setting up a fabric sample for digitalization on a stretch testing machine
Mechanical Parameters are influenced by the material of the yarns, the structure of the fabric, the tension of the loom, the dye, the coating, and other construction parameters. Each fabric is different, and has therefore different Mechanical Parameters. In order to capture the Mechanical Parameters of a particular fabric, one has to digitalize it.
This is usually done by running physical samples of the fabric through a series of mechanical tests using special machines that will weight, stretch and bend the fabric in different directions. This process is manual, long, expensive, and has to be repeated for each new fabric.
However, it’s the only way today to properly capture the Mechanical Parameters of a fabric sample.
Or is it? At Seddi, we have been working on a new, groundbreaking approach to fabric digitalization, free of expensive machines and of tedious manual labor. Leveraging the power of AI and our database of thousands of digitalized materials, we are able to predict the Mechanical Parameters of any fabric from a single scanned image and a few easy-to-find bits of information about the fabric. And we can do this in the time it takes to make and drink a cup of coffee. No need to follow complex procedures, ship physical samples to the other side of the world, or wait several weeks. Stay tuned.