Some software applications claim to reduce the volume of physical samples that the fashion industry produces. Fashion professionals, however, have an affinity for the tactile, dynamic nature of physical prototypes. How does an industry built on movement and texture let go of the sensory to embrace more sustainable and flexible solutions that technology has to offer? In this article, find out:
- New technological innovations that reduce physical fabric sampling
- Why now is the time for brands, mills, and manufacturers to move toward 3D sampling
- How accurate digital fabrics can help bridge the gap between the tactile nature of fashion and digital design processes
To captivate the fashion community, we must create convincing, accurate 3D samples that go beyond an artistic 3D model. They must look photographically identical to the fabrics that arrive in bulk production. SEDDI’s technology creates a mechanically and optically accurate virtual fabric sample that moves and appears like the real textile. Early adopters of these kinds of innovative solutions will progress more quickly toward the efficient and sustainable future of the fashion industry.
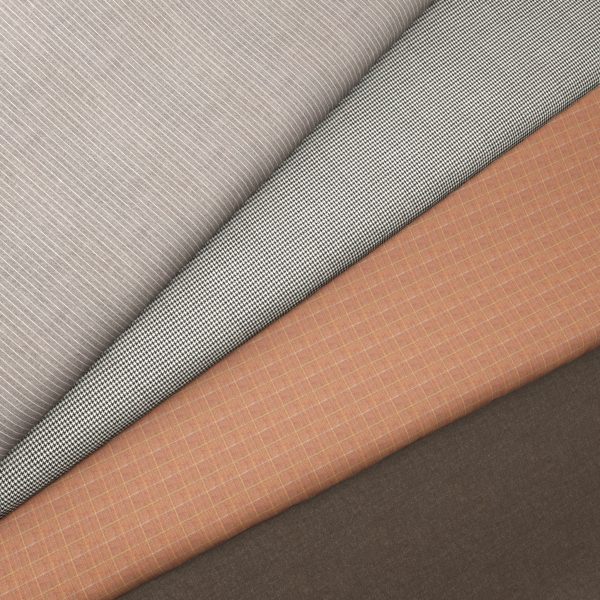
3D Fabric from Textura
What Does 3D Virtual Sampling Mean for Business and the Environment?
The push toward replacing physical samples with 3D samples stems from several driving factors. First, the rise of supply chain disruption has shown us how quickly our best laid plans can go awry. The already time and resource-intensive process of sampling becomes even more so when things go wrong. Challenged by the shift towards remote working and an increase in natural disasters, pandemics, and political unrest, brands need a backup plan. 3D sampling with SEDDI’s technology offers that safety net without compromising quality and accuracy.
Additionally, the turnaround time to make and receive physical fabric samples—just to eliminate or change designs completely—is terribly inefficient. The fashion industry needs to be able to react quickly when consumers are ready to spend. Between inflation and the state of the economy, brands need to be ready to jump on opportunities when there is even a slight upswing in consumer confidence. It’s not sensible to spend weeks and weeks spinning, weaving, cutting, sewing, and shipping samples back and forth across the ocean before production can even begin.
Finally, it’s no secret that fashion has a history of waste. 3D sampling saves time and reduces small parcel shipments of swatches around the globe for trials and testing. The use of 3D samples increases timely collaboration across regions and between colleagues who may be remote.
Why Can’t the Apparel Industry Let Go of the Tactile Nature of Fashion?
Part of what draws people to fashion as an art form is that it is made for the human body. It envelops us, touches us, and enables us to express ourselves outwardly without words. Of course, it is a tall order to convince fashion creatives to let go of the tactile nature of sampling, as fashion has always been physical. Changing the mindset of an entire industry is a difficult endeavor.
Does adopting 3D sampling mean the fashion industry has to break up with texture and touch? Do we bank on what’s on the screen and hope it feels good in our hands? The truth is, it’s not all or nothing. Many industries, such as cars and electronics have already successfully adopted digital design solutions that enhance physical design processes. In order for fashion professionals to follow suit and accept digital fabrics as reliable samples, 3D materials must be accurate and evoke the emotion and satisfaction that real materials do. 3D cloth must move and flow and gather the way real cloth does. There should be no question of how fabric will behave or feel.
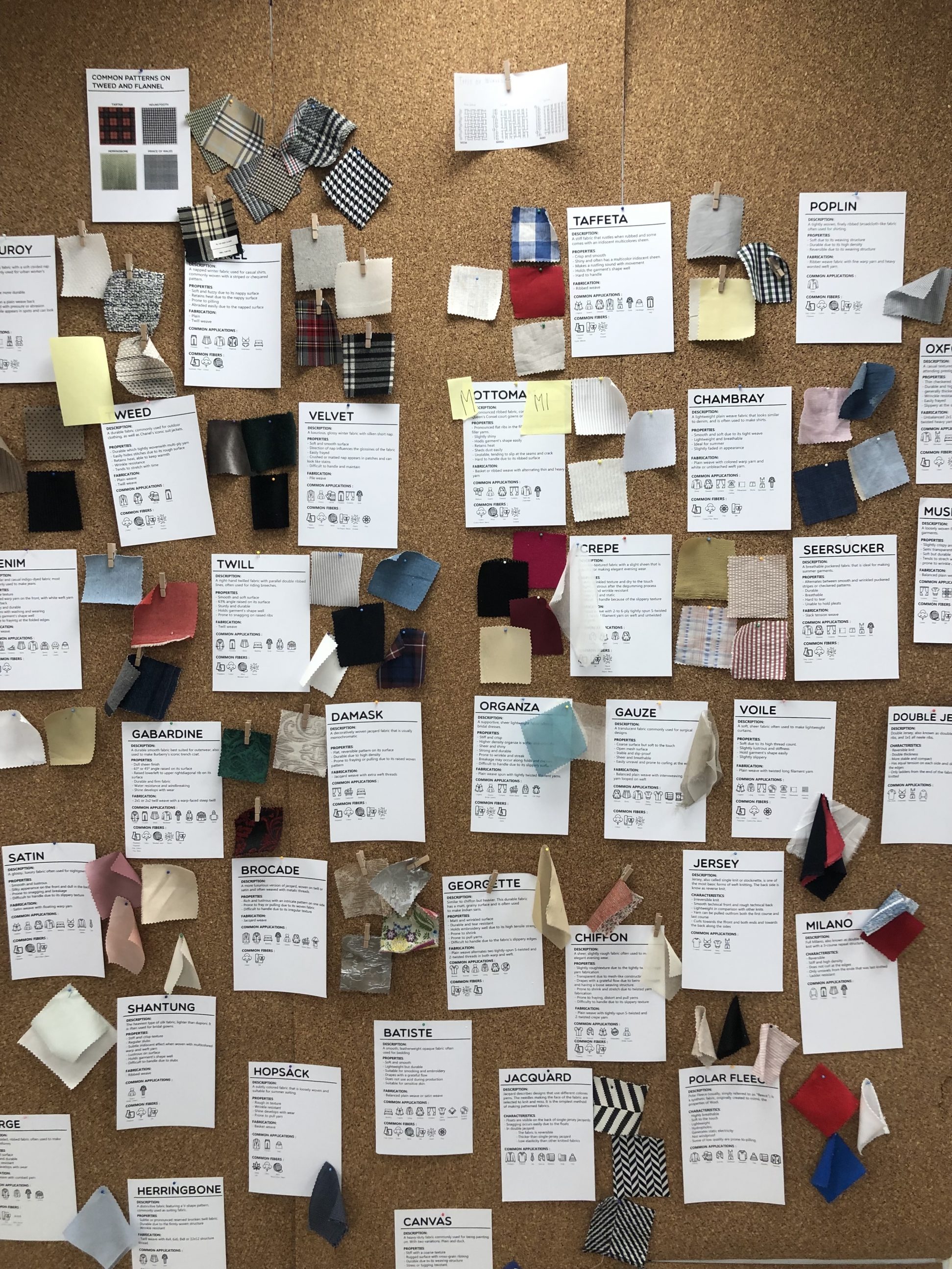
SEDDI has captured thousands of fabric samples to train its AI
We don’t have to let go of the sensory aspect of fashion—we have to learn to see the accurate simulation shown before us on the screen as if it’s actually there. Reducing physical samples down to one would yield tremendous gains in efficiency and time, all while preserving the tactile experience in the next phase of design. 3D technology must fully prove itself before all samples are routinely eliminated. We have to learn to trust that virtual samples are correct, and that when the physical sample arrives for final approval, it will be representative of what we’ve previewed. Due to its science-based simulation technology, the company that is poised to drive this shift in the industry is SEDDI.
How Digital Fabrics Created in SEDDI Textura Solve Digital and Physical Needs
SEDDI’s technology can reduce physical fabric sampling and satisfy the fashion industry’s desire for the physical properties of apparel. SEDDI’s computer scientists have developed robust AI that takes into account both the visual properties (appearance, structure, texture, lighting) and mechanical properties (movement, stretch, bend) of textiles, resulting in accurate, high-quality digital fabric samples.
Some fashion professionals may lack the trust necessary to transition to 3D sampling because earlier technological iterations were insufficient. SEDDI has moved the technology from artistic interpretation to accurate simulation due to the company’s extensive research, innovation, and development of the rich data that inform SEDDI’s AI. Thousands of materials have been analyzed so that even if a new fabric is introduced by the user, SEDDI Textura can predict within a small margin of error how it will behave and appear on the human form. These digital fabrics can then be used in 3D CAD software to construct a garment.
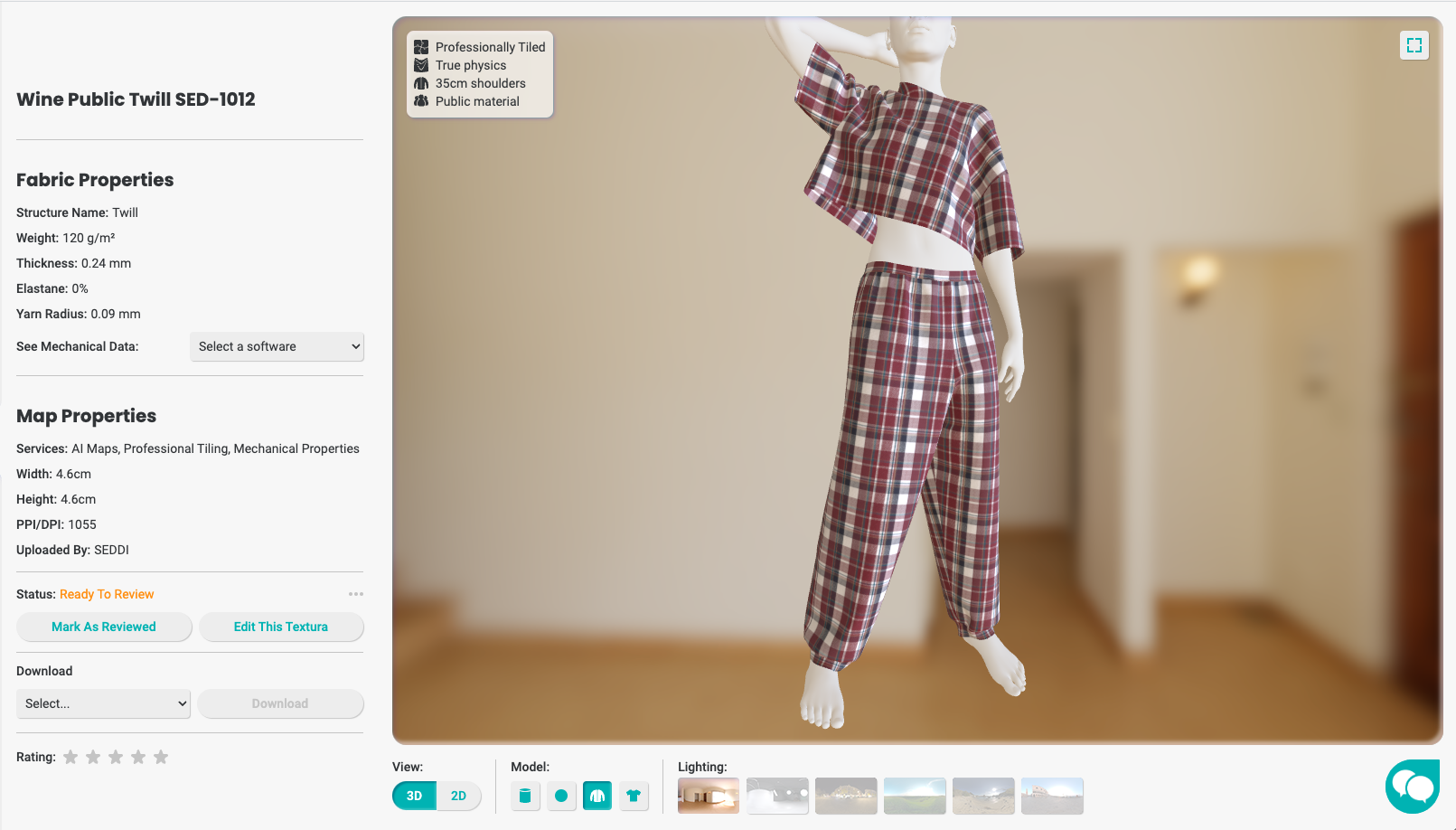
SEDDI Textura’s 3D Viewer
Accurate Digital Fabric is the Answer
It’s important to be discerning with what 3D fabric digitalization solution you choose, because when it comes to reducing and/or replacing physical samples with digital fabrics, what you see is not always what you get. If textiles are not accurately modeled, it is not possible to adopt digital fabrics en masse as an alternative to sampling. SEDDI goes beyond generic, illustrative shapes, curves, and shadows for digital fabric visualization to truly bring fashion fabrics to life and reduce the industry’s reliance on physical samples. With SEDDI Textura fabric digitalization technology at hand, the fashion industry can react, create, simplify, and bring products to market in a more efficient way.
Everyone wins—businesses, humanity, and the environment.
Curious about how SEDDI Textura can improve your company’s sampling process?